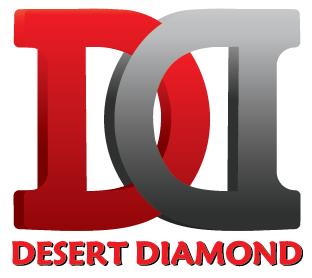
Float Collar
Desert Diamond International provides a range of essential oil field tools, including the Float Collar, which plays a vital role in well cementing operations. The float collar is a key component in the casing string, positioned just above the float shoe. It serves multiple critical functions during the cementing process in oil and gas wells.
Functions and Applications of Float Collar
The float collar primarily functions as a landing point for cementing plugs and as a one-way valve to prevent the backflow of cement slurry into the casing once the pumping stops. This ensures that the cement is properly placed in the annulus between the casing and the wellbore, which is essential for well integrity. The float collar is particularly useful in:
Functions and Applications of Float Collar
The float collar primarily functions as a landing point for cementing plugs and as a one-way valve to prevent the backflow of cement slurry into the casing once the pumping stops. This ensures that the cement is properly placed in the annulus between the casing and the wellbore, which is essential for well integrity. The float collar is particularly useful in:
Preventing Cement Backflow
The integral one-way valve in the float collar allows fluids to flow down the casing but revents any return flow, thereby ensuring that the cement remains in place during the setting process.
Supporting Cementing Plugs
The float collar acts as a landing point for the bottom and top cementing plugs. This ensures proper displacement of the cement slurry and provides a clear indication when the ementing process is complete.
Maintaining Well Control
By preventing the backflow of fluids, the float collar helps maintain control over the well uring the critical cementing phase, which is rucial for avoiding blowouts or other well control issues.
Sizes and Specifications
Float collars are available in a range of sizes to accommodate different casing diameters. Common sizes include:
- 2 7/8 inches
- 4 1/2 inches
- 7 inches
- 9 5/8 inches
- 13 3/8 inches
- 20 inches
Additionally, custom sizes can be manufactured to meet specific well requirements. These collars are designed to handle high pressures, with standard models rated up to 10,000 psi, while some can withstand pressures up to 15,000 psi depending on the application and well conditions.
Material Specifications
Float collars are made from a variety of materials, depending on the specific requirements of the well:
Casing Grade Steel
This is the most common material used for the body of the float collar. The steel is often seamless and can be provided in grades like K-55, L-80, N-80, C-95, T-95, and P110, which are selected based on the well's pressure and temperature conditions.
Composite Materials
In some applications, particularly where easy drill-out is required, components such as the valve are made from composite materials like glass-reinforced epoxy resin. These materials are lightweight, drillable, and resistant to the harsh downhole environment.
Aluminum
Aluminum valves are also used in certain esigns, offering a balance of strength and drillability.
Types of Float Collars
Float collars can be classified based on their valve types and specific applications:
Conventional Float Collar
Typically equipped with a single or double valve system, these are used in most vertical, horizontal, and deviated wells. They are designed to prevent backflow and maintain well control during the cementing process.
Non-Rotating Float Collar
This type includes an anti-rotation feature that improves drill-out performance and is used in wells where precise placement and stability re critical.
Latch-In and Stab-In Float Collars
These types are used for more specialized operations, such as where casing needs to be joined securely without rotation, or in wells ith unique geometric challenges.
Application in Different Types of Wells
Float collars are versatile and can be used in various types of oil wells:
Vertical Wells
Standard float collars are sufficient to guide the casing and prevent cement backflow.
Horizontal and Deviated Wells
These wells often require non-rotating or latch-in float collars to ensure proper sealing and casing placement despite the well's trajectory.
High-Pressure High-Temperature (HPHT) Wells
In these extreme conditions, float collars made from high-strength steel and advanced valve materials are necessary to withstand the pressures and temperatures encountered.
Desert Diamond International ensures that their float collars are designed to meet the rigorous demands of different well types, enhancing well integrity and ensuring the success of cementing operations. This careful selection of materials and designs allows for reliable performance in a wide range of drilling environments.